When Autonomous Maintenance Occurs: Timing and Strategy with Weever's Assistance
Discover when to perform autonomous maintenance and how Weever's tools help businesses optimize timing, automate tasks, and stay ahead of industry trends.
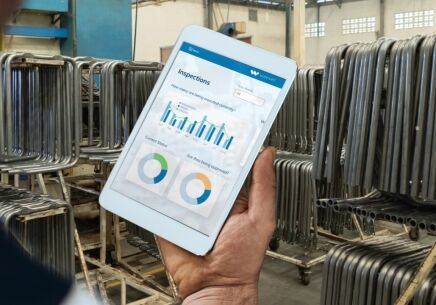
Autonomous maintenance, an essential pillar of Total Productive Maintenance (TPM), empowers operators to take charge of routine maintenance tasks such as cleaning, inspecting, and lubricating equipment. However, one of the most important aspects of successful autonomous maintenance is knowing when these activities should occur to maximize effectiveness and align with the latest industry trends.
So, when should autonomous maintenance occur, and how can Weever software help businesses determine the best timing while staying agile in an ever-evolving industry? Let's explore the key moments for autonomous maintenance and how Weever ensures timely and efficient execution of these practices.
Understanding When Autonomous Maintenance Should Occur
The timing of autonomous maintenance is critical for preventing equipment breakdowns, extending the lifespan of machinery, and optimizing overall production. Key moments when autonomous maintenance should occur include:
- At Regular Intervals: Maintenance tasks should be scheduled at regular intervals based on equipment usage and manufacturer recommendations. These regular tasks, such as cleaning and lubricating, help keep equipment in optimal working condition. Weever software can help automate these tasks and schedules.
- After Specific Equipment Cycles: For machinery that operates in cycles, autonomous maintenance should occur after a certain number of cycles to prevent wear and tear from accumulating unnoticed.
- Following an Anomaly: If operators detect unusual noises, vibrations, or performance drops, autonomous maintenance should be initiated to inspect and address potential issues before they lead to a breakdown. Weever software allows for real-time reporting of such issues, helping managers and strategists to detect patterns in anomalous behavior.
- In Alignment with Emerging Trends: New trends and technologies may introduce improved maintenance practices or new tools for inspecting and repairing equipment. Businesses should be prepared to adjust their maintenance schedule as industry standards evolve. Weever software is highly configurable, allows for agile changes to new processes, methodologies, and trends.
Determining the right timing for these activities is critical to ensuring that equipment runs smoothly and efficiently. This is where Weever software comes into play, providing the tools businesses need to optimize the timing of their autonomous maintenance strategies and stay ahead of industry trends.
How Weever Ensures Timely and Strategic Autonomous Maintenance
Weever software offers a suite of features designed to help businesses determine the optimal timing for autonomous maintenance, automate routine tasks, and adapt to emerging trends. Here's how Weever facilitates this process:
1. Ease of Use: Simplifying Timing and Strategy
One of the key challenges in implementing autonomous maintenance is determining the best timing for routine tasks without overwhelming operators. Weever's intuitive platform makes it easy for businesses to establish and adjust the timing of autonomous maintenance activities, ensuring that they are carried out at the right intervals and in line with current industry standards.
With Weever, businesses can create and manage maintenance schedules that are aligned with equipment usage and operational goals. The platform's ease of use ensures that operators can quickly understand and implement these schedules, minimizing confusion and ensuring that maintenance tasks are performed on time. Weever's flexibility also allows businesses to easily adjust schedules as new trends emerge, ensuring that they remain competitive and efficient.
2. Automated Workflows and Action Items: Streamlining Maintenance Tasks
Weever takes the guesswork out of scheduling and executing autonomous maintenance tasks by automating key workflows. By setting up automated action items, businesses can ensure that routine maintenance tasks are performed consistently and without manual intervention.
For example, Weever allows businesses to automate the scheduling of inspections, cleanings, and lubrication tasks based on predetermined intervals or equipment usage metrics. This automation not only ensures that maintenance is performed at the right time but also reduces the burden on operators and managers by eliminating the need for constant manual oversight.
Additionally, by automating these workflows, Weever allows businesses to stay aligned with the latest trends in autonomous maintenance. As new industry practices or technologies emerge, Weever can seamlessly integrate them into existing workflows, ensuring that businesses remain ahead of the curve without disrupting operations.
3. Insights and Trends: Leveraging Data for Proactive Maintenance
Weever's advanced analytics tools provide businesses with valuable insights into the effectiveness and timing of their maintenance activities. By analyzing data from ongoing maintenance tasks, Weever helps businesses identify the optimal moments for performing autonomous maintenance, ensuring that tasks are carried out before equipment issues arise.
These insights also allow businesses to track industry trends and adjust their maintenance strategies proactively. By staying informed about emerging practices, businesses can ensure that their maintenance schedules are aligned with the latest technologies and methodologies, helping them stay competitive in a rapidly changing landscape.
Weever's analytics not only help businesses maintain their current equipment but also prepare for future trends. With this data, businesses can anticipate changes in maintenance needs and make strategic adjustments to their schedules, ensuring that they remain efficient and effective as industry standards evolve.
4. Real-Time Reporting: Staying Agile and Informed
In the fast-paced world of industrial operations, real-time information is key to making informed decisions about maintenance. Weever's real-time reporting features allow businesses to track the status of their maintenance activities and make adjustments as needed.
For example, if an operator identifies an issue during routine maintenance, Weever's real-time reporting can immediately alert managers, enabling them to take swift corrective action. This capability ensures that businesses can respond quickly to emerging trends or changes in equipment performance, minimizing downtime and ensuring that equipment remains in peak condition.
Weever's real-time reporting also allows businesses to monitor the effectiveness of their maintenance schedules. By tracking key metrics such as task completion rates, equipment performance, and downtime, businesses can continuously improve their maintenance strategies and stay ahead of industry trends.
5. Rollout Methodology: Ensuring Efficient Implementation of Maintenance Strategies
Implementing and adjusting autonomous maintenance schedules can be a complex process, especially as new trends emerge. Weever's structured rollout methodology ensures that businesses can efficiently implement and adjust their maintenance strategies without causing disruptions to daily operations.
Weever provides a clear roadmap for rolling out new maintenance initiatives, from initial planning to full deployment. This structured approach ensures that businesses can quickly adapt to new trends and technologies while maintaining operational efficiency. Whether introducing a new maintenance schedule or incorporating emerging best practices, Weever's rollout methodology ensures a smooth transition, keeping businesses ahead of the competition.
Maintaining Equipment Efficiency and Downtime with Weever
Autonomous maintenance is a critical aspect of maintaining equipment efficiency and minimizing downtime. However, knowing when to perform these tasks is just as important as performing them correctly. By leveraging Weever software, businesses can ensure that their autonomous maintenance activities are performed at the optimal times, keeping equipment in peak condition and staying ahead of industry trends.
With its ease of use, automated workflows, advanced insights, real-time reporting, and structured rollout methodology, Weever helps businesses streamline their maintenance strategies and remain competitive in an ever-changing industrial landscape.
Optimize Autonomous Maintenance with the right timing and strategy. See how Weever helps streamline your operations. Learn more!
Optimize Autonomous Maintenance with the right timing and strategy. See how Weever helps streamline your operations. Learn more!
Continue Reading
"Having cloud-based forms on devices around the facility makes them so much more accessible, which makes it painless for operators to quickly provide a report."
Johanna Velez, VP Quality Assurance
"Weever is really user friendly and will have a massive positive impact on our operations and training team."
Mel Cadle - Op Ex Lead Process Engineer
"It's shifted our safety culture because now we are much more focused on what we should be looking at."
Kody Crossen, Operations Manager of EHS