Building an Autonomous Maintenance Checklist: How Weever Simplifies the Process
Build an effective autonomous maintenance checklist with Weever. Simplify management, automate tasks, gain insights, and stay ahead of trends.
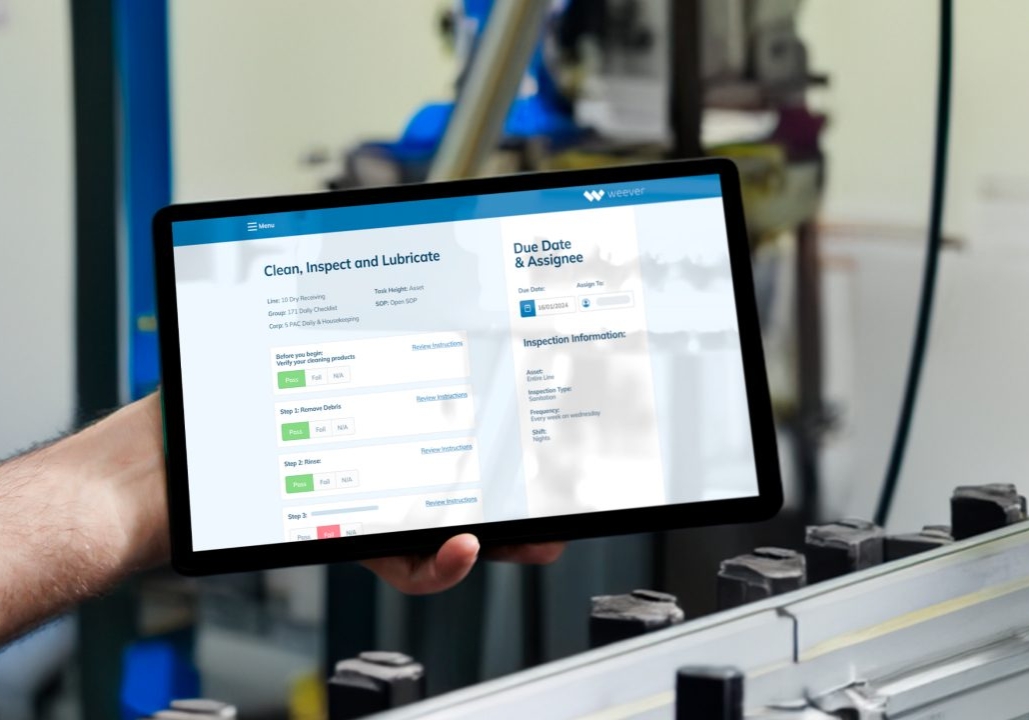
Maintaining equipment reliability and efficiency is more crucial than ever. Autonomous maintenance, a key component of Total Productive Maintenance (TPM), empowers operators to take ownership of routine maintenance tasks, reducing downtime and ensuring that machinery operates at peak performance. However, to fully realize the benefits of autonomous maintenance, businesses must develop a detailed and effective checklist that guides operators through each maintenance activity. This checklist is not just a set of tasks but a dynamic tool that evolves with emerging trends and technological advancements.
So, how can businesses build an effective autonomous maintenance checklist, and how does Weever software help them stay ahead of these trends? Let's explore.
Building an Effective Autonomous Maintenance Checklist
Creating a comprehensive autonomous maintenance checklist involves several key steps, each designed to ensure that all necessary tasks are identified, standardized, and efficiently executed. Below is a detailed checklist that businesses can use as a starting point:
1. Initial Cleaning
Task: Thoroughly clean the equipment to remove all contaminants such as dust, dirt, oil, and grease.
Purpose: Initial cleaning helps operators familiarize themselves with the equipment and identify any issues like leaks or wear that might be hidden under grime.
Weever's Role: Weever simplifies the scheduling and tracking of initial cleaning tasks. The platform allows businesses to create specific cleaning protocols that can be easily followed by operators, ensuring consistency and thoroughness.
2. Eliminate Contamination Sources
Task: Identify and eliminate the sources of contamination that could affect equipment performance, such as fixing leaks, sealing openings, and improving workplace cleanliness.
Purpose: Preventing recontamination ensures that the initial cleaning is effective and that equipment stays in optimal condition longer.
Weever's Role: Weever can automate reminders and action items related to eliminating contamination sources. By setting up automated workflows, businesses ensure that operators address contamination risks proactively, reducing the chances of equipment degradation.
3. Establish Cleaning, Inspecting, and Lubrication (CIL) Standards
Task: Develop standardized procedures for cleaning, inspecting, and lubricating equipment. Define the tools, materials, and frequency for each task.
Purpose: Standardization ensures that maintenance tasks are performed consistently, reducing variability in equipment performance.
Weever's Role: With Weever, businesses can easily create and manage CIL standards within their autonomous maintenance checklists. The platform's intuitive interface allows for quick updates and modifications, ensuring that new trends and best practices are seamlessly incorporated into the checklist.
4. General Inspections
Task: Conduct regular inspections to identify abnormalities or potential issues, such as unusual noises, vibrations, or temperature changes.
Purpose: Early detection of issues prevents small problems from escalating into major failures, reducing downtime and repair costs.
Weever's Role: Weever automates the scheduling of general inspections and tracks their completion. Real-time alerts and notifications ensure that no inspections are missed, and any identified issues are promptly addressed.
5. Autonomous Inspection
Task: Empower operators to conduct detailed inspections using specialized tools and techniques, enabling them to detect early signs of wear, misalignment, or other issues.
Purpose: Autonomous inspections deepen operators' understanding of their equipment, allowing them to take a more active role in maintenance.
Weever's Role: Weever supports autonomous inspections by providing operators with easy access to digital checklists and inspection guides. The platform can also integrate with IoT devices to automatically log inspection data, making the process more efficient and accurate.
6. Standardization of Best Practices
Task: Document all procedures, inspections, and maintenance tasks to ensure that best practices are consistently followed across the organization.
Purpose: Standardization reduces variability and ensures that all operators are performing maintenance tasks at the same high standard.
Weever's Role: Weever allows businesses to document and standardize all maintenance practices within a digital platform. This documentation can be easily updated as new trends and technologies emerge, ensuring that the checklist remains relevant and effective.
7. Continuous Improvement
Task: Regularly review and refine maintenance practices based on feedback, new insights, and industry trends.
Purpose: Continuous improvement ensures that maintenance practices evolve with technological advancements, keeping equipment at peak performance.
Weever's Role: Weever's analytics and reporting tools provide businesses with the data needed to identify areas for improvement. By leveraging these insights, businesses can continuously update their checklists to incorporate the latest maintenance trends and technologies.
How Weever Helps Businesses Stay Ahead of Emerging Trends
Creating and managing an autonomous maintenance checklist is just the beginning. To truly excel in maintenance practices, businesses must also ensure that their checklists evolve with industry trends. Weever software is designed to help businesses not only build effective checklists but also stay ahead of emerging trends through several key features:
1. Ease of Use: Simplifying Checklist Management
Weever's intuitive platform makes it easy for businesses to create and manage comprehensive autonomous maintenance checklists. The software's user-friendly interface allows operators and managers to quickly update tasks, incorporate new trends, and ensure that all maintenance activities are aligned with current industry standards. This ease of use is critical for maintaining a dynamic checklist that evolves as new technologies and methodologies emerge.
2. Automated Workflows and Action Items: Enhancing Efficiency
One of the biggest challenges in maintaining an effective checklist is ensuring that all tasks are executed consistently and on time. Weever automates the execution of checklist items, allowing businesses to focus on strategic improvements rather than getting bogged down by routine tasks. Automated workflows ensure that even the latest trends in autonomous maintenance are consistently applied, helping businesses maintain high levels of operational efficiency.
3. Insights and Trends: Staying Ahead of the Curve
Weever's advanced analytics provide businesses with data-driven insights into their maintenance practices. By analyzing trends and identifying areas for improvement, Weever helps businesses incorporate emerging trends into their checklists. This proactive approach ensures that businesses stay competitive and maintain their equipment at optimal levels.
4. Real-Time Reporting: Staying Informed and Agile
In the fast-paced world of industrial maintenance, staying informed is crucial. Weever's real-time reporting features keep businesses up to date on the status of their maintenance checklists. Whether it's tracking the completion of tasks or monitoring the effectiveness of new strategies, real-time reporting allows businesses to adjust quickly to new industry developments. This agility is key to maintaining operational efficiency and staying ahead of the competition.
5. Rollout Methodology: Smooth Integration of New Trends
Introducing new trends into an established maintenance routine can be challenging. Weever's structured rollout methodology ensures that new trends are smoothly integrated into existing checklists without causing disruption. By providing a clear roadmap for implementation, Weever helps businesses optimize their maintenance operations while staying current with the latest industry developments.
An Evolving Checklist for Emerging Trends and Technologies
Building an effective autonomous maintenance checklist is essential for maintaining equipment reliability and efficiency. However, the real challenge lies in ensuring that this checklist evolves with emerging trends and technologies. Weever software provides businesses with the tools they need to create, manage, and continuously improve their maintenance checklists. With features like ease of use, automated workflows, data-driven insights, real-time reporting, and a structured rollout methodology, Weever helps businesses stay ahead of the curve and maintain their competitive edge in an ever-changing industrial landscape.
Take the next step in streamlining-ask for details now!
Take the next step in streamlining-ask for details now!
Continue Reading
"Having cloud-based forms on devices around the facility makes them so much more accessible, which makes it painless for operators to quickly provide a report."
Johanna Velez, VP Quality Assurance
"Weever is really user friendly and will have a massive positive impact on our operations and training team."
Mel Cadle - Op Ex Lead Process Engineer
"It's shifted our safety culture because now we are much more focused on what we should be looking at."
Kody Crossen, Operations Manager of EHS