Reducing Defects through Proactive Monitoring with Weever’s Abnormality and Defect Detection
Reduce defects with Weever's proactive monitoring. Detect abnormalities early, automate resolutions, and improve product quality with real-time insights.
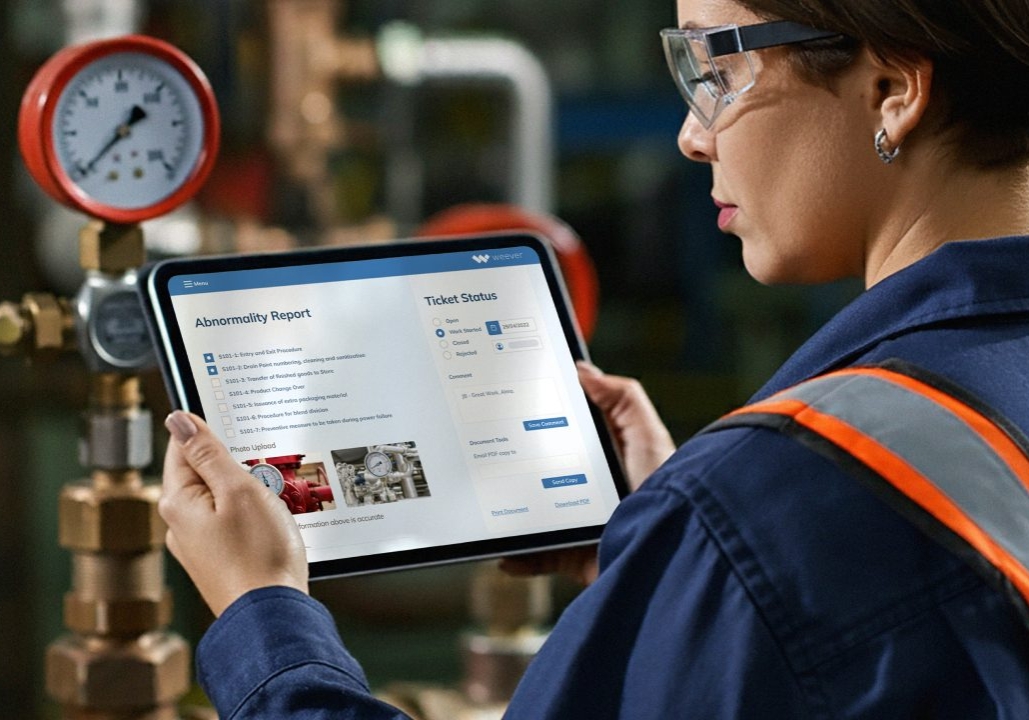
The smallest defect can have costly ripple effects in manufacturing operations, leading to product recalls, dissatisfied customers, and lost revenue. Manufacturers need a way to proactively identify and address issues before they escalate. Enter Weever’s abnormality and defect detection – a cutting-edge approach that transforms how manufacturers monitor and resolve quality issues.
This blog explores the question: How does proactive monitoring with Weever’s abnormality and defect detection reduce defects and improve product quality? Let’s dive in to uncover the answer.
The Challenge: Why Defect Prevention is Critical
Modern production environments operate at a breakneck pace, leaving little room for error. Yet, even the most sophisticated processes are not immune to abnormalities that can lead to defects. These issues can stem from equipment malfunctions, human errors, or process deviations.
Traditional defect management often relies on reactive measures, addressing issues only after they’ve disrupted production or tarnished a product. This approach not only increases costs but also risks reputational damage. Proactive monitoring, particularly with Weever’s specialized tools, flips the script, allowing manufacturers to anticipate and eliminate defects before they become problems.
Proactive Monitoring: The Key to Superior Product Quality
Proactive monitoring leverages real-time data and predictive insights to identify abnormalities at their earliest stages. By doing so, manufacturers can intervene promptly, reducing defect rates and improving overall product quality. Weever’s abnormality and defect detection solution is uniquely positioned to drive this shift.
But what sets Weever apart? Let’s explore the features that make it an indispensable tool for proactive monitoring.
Simplicity at Weever’s Core
In the fast-paced manufacturing world, tools that are cumbersome or complex are unlikely to gain traction. That’s why Weever’s platform is designed with intuitive usability at its core.
Setting up proactive monitoring for abnormalities and defects is straightforward, enabling teams to get started without a steep learning curve. The software allows users to configure custom workflows, define defect parameters, and deploy monitoring protocols with ease. This simplicity ensures quick adoption and boosts confidence among staff at all levels.
Seamless Automation Abnormality and Defect Management
Time is of the essence when abnormalities arise. Weever automates the detection process, flagging issues as soon as they occur. The software assigns corrective action items to the appropriate teams, ensuring swift resolution.
Automation doesn’t stop there. Weever’s proactive monitoring capabilities integrate seamlessly with existing workflows, reducing manual intervention and minimizing the chances of human error. By closing the loop between detection and resolution, manufacturers can prevent small abnormalities from snowballing into full-blown defects.
Data-Driven Excellence with Real-Time Insights and Reporting
Understanding the “why” behind defects is as important as addressing them. Weever provides manufacturers with rich insights into defect patterns and trends. By analyzing historical data, the software identifies recurring issues, empowering teams to implement long-term improvements.
Weever’s real-time reporting is a game-changer, offering visibility into abnormalities and defects as they happen. This immediacy allows teams to respond in the moment, minimizing the impact on production quality. Over time, these insights drive a culture of continuous improvement, where data-informed decisions become the norm.
Scalable Solutions: Deploying Weever Across Operations
Rolling out proactive monitoring across multiple production lines can be daunting. Weever simplifies this process with its strategic rollout methodology, ensuring smooth implementation and consistent quality control, in as little as three weeks.
Whether you’re managing a single facility or a global network of plants, Weever ensures that every production line benefits from the same high standards. Its adaptable framework accommodates diverse operational needs, making it the ideal solution for organizations of any size.
The Results: Fewer Defects, Higher Quality, Happier Customers
The impact of integrating proactive monitoring with Weever’s abnormality and defect detection is transformative for manufacturers. By detecting issues at their earliest stages and taking swift corrective action, production lines experience a dramatic reduction in defect rates. This early intervention not only prevents small problems from escalating but also ensures that production processes run more efficiently, minimizing waste and downtime.
As a result, product quality reaches new heights. With continuous monitoring in place, manufacturers can consistently deliver goods that meet or exceed industry standards. This commitment to excellence resonates with customers, fostering trust and loyalty while enhancing the company’s reputation in the marketplace. Furthermore, addressing abnormalities proactively translates to significant cost savings, as manufacturers avoid the financial and operational burden of large-scale recalls or defect-related disruptions.
Ultimately, the combination of fewer defects, superior product quality, and improved customer satisfaction positions manufacturers to thrive in a competitive landscape. Weever’s solution empowers teams to not only solve problems but also build a future rooted in consistent quality.
A Future Without Defects Starts Here
Proactive monitoring isn’t just a strategy; it’s a commitment to excellence. With Weever’s abnormality and defect detection solution, manufacturers can transform their approach to quality control, reducing defects and elevating product standards.
Ready to experience the difference for yourself? Contact Weever today for a demo and take the first step toward defect-free manufacturing.
Discover how proactive monitoring can transform your manufacturing processes.
Discover how proactive monitoring can transform your manufacturing processes.
Continue Reading
"Having cloud-based forms on devices around the facility makes them so much more accessible, which makes it painless for operators to quickly provide a report."
Johanna Velez, VP Quality Assurance
"Weever is really user friendly and will have a massive positive impact on our operations and training team."
Mel Cadle - Op Ex Lead Process Engineer
"It's shifted our safety culture because now we are much more focused on what we should be looking at."
Kody Crossen, Operations Manager of EHS