How Frontline Workers Can Streamline Maintenance Routines Using Weever's Connected Worker Platform
Streamline maintenance routines with Weever's Connected Worker Platform. Empower frontline workers with automated workflows, real-time reporting, and visual task controls.
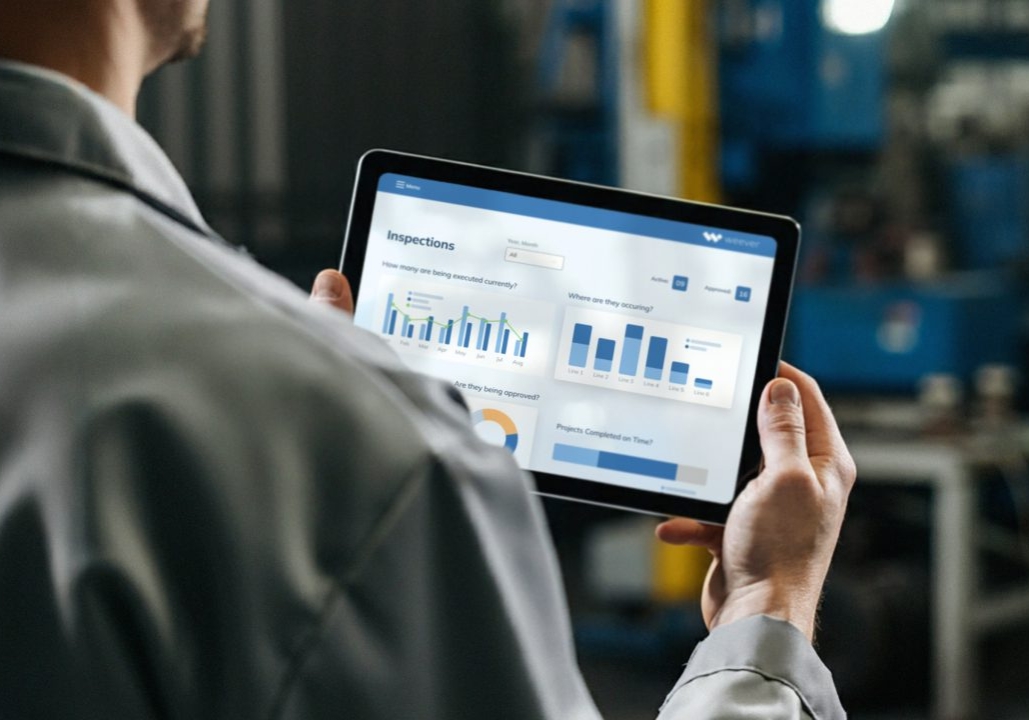
In industries such as food production, retail, logistics, and healthcare, maintaining smooth operations and reducing downtime are critical to success. However, managing maintenance tasks on the frontlines can be challenging without the right tools, leading to missed tasks, equipment breakdowns, and reduced efficiency. Frontline worker maintenance-where operators take charge of daily maintenance activities-can transform this process, but only if supported by effective tools.
Enter Weever's Connected Worker Platform: a robust solution designed to streamline maintenance routines for frontline workers. Weever empowers operators to handle preventive and routine maintenance efficiently, through operator-led maintenance, where they follow tasks such as cleaning standards, inspection routines, and lubrication schedules. With Weever, workers have access to automated workflows, real-time reporting, and visual controls that simplify maintenance tasks.
How Can Frontline Workers Streamline Maintenance Routines Using Weever's Connected Worker Platform?
The Weever platform is a comprehensive solution that simplifies the management of maintenance tasks, allowing frontline workers to take control of their daily routines without the need for extensive technical knowledge. Below, we explore how Weever helps frontline workers streamline maintenance processes, providing them with the tools to increase productivity, improve compliance, and minimize downtime.
Empowering Frontline Workers with an Intuitive Platform
One of the key challenges in operator-led maintenance is making sure that workers can easily navigate and manage maintenance tasks. Many frontline workers don't have extensive technical training, so the platform they use must be accessible and intuitive.
Weever's Connected Worker Platform addresses this challenge with a user-friendly interface designed for simplicity:
- Intuitive Navigation: Workers can easily access the tasks they need to complete, whether it's checking CIL checklists (Cleaning, Inspection, Lubrication), following CIL standard operating procedures (SOPs), or viewing upcoming lubrication schedules.
- Minimal Training Required: The platform provides CIL training for operators that ensures they can quickly understand the necessary maintenance processes. Workers don't need specialized skills or extensive onboarding to execute preventive maintenance by operators. This allows them to efficiently handle maintenance tasks like cleaning standards or inspection routines without delays.
- Tailored for Various Industries: Whether working in food production, logistics, or healthcare, Weever can be customized to fit the specific requirements of each sector. For example, workers in retail can follow digitized CIL instructions to maintain refrigeration systems, while those in logistics can track conveyor belt maintenance with ease.
Weever empowers workers to take responsibility for their maintenance tasks, enhancing productivity and operational efficiency with an intuitive and accessible platform.
Streamlining Maintenance Routines
Managing multiple maintenance tasks and ensuring they're completed on time can be overwhelming without a structured process in place. Weever's automated workflows remove the guesswork from frontline worker maintenance, ensuring that all tasks are completed consistently and efficiently.
- Automated Task Assignment: Weever automatically schedules and assigns tasks to frontline workers, whether it's following inspection routines, lubrication schedules, or adhering to cleaning standards. This ensures that preventive maintenance tasks are completed on time, reducing the likelihood of equipment failures.
- Clear Action Items: Each worker is assigned clear and actionable maintenance tasks, such as completing a CIL checklist or following a CIL SOP. Workers are alerted to upcoming or overdue tasks, allowing them to prioritize maintenance effectively.
- Real-Time Notifications: Weever provides real-time notifications to workers and managers when a task is due or missed, ensuring that preventive maintenance by operators is carried out consistently. This feature helps avoid gaps in maintenance that could lead to equipment downtime or compliance issues.
By automating workflows and providing real-time action items, Weever ensures that frontline workers can stay on top of their tasks without manual oversight, streamlining the entire maintenance process.
Data-Driven Decision Making for Maintenance
In order to maintain equipment reliability and ensure that maintenance routines are effective, frontline workers need access to data and insights about their equipment's performance. Weever's Connected Worker Platform offers valuable insights and real-time reporting tools that help workers and managers stay informed and make proactive decisions.
- Tracking Maintenance Performance: Weever enables frontline workers to track their maintenance activities using data-driven insights. By tracking CIL with connected worker platforms, workers and managers can monitor equipment health, track task completion, and identify areas where preventive maintenance may be lacking.
- Identifying Recurring Issues: Weever's insights dashboard helps identify recurring issues with specific equipment, such as frequent breakdowns or recurring lubrication needs. For instance, if a machine regularly fails its CIL checklist, operators can adjust their lubrication schedules or inspections to mitigate the issue before it becomes a larger problem.
- Real-Time Reporting: Weever's real-time reporting feature gives frontline workers instant visibility into the status of their maintenance tasks. Workers and managers can quickly see which tasks have been completed, which are overdue, and which may require immediate attention. This helps ensure that preventive maintenance by operators is always on track, minimizing downtime and keeping equipment in top condition.
Weever helps workers and managers stay ahead of issues, making data-driven decisions that improve overall performance and ensure compliance with cleaning standards and other regulatory requirements.
Seamlessly Integrating Weever's Connected Worker Platform
One of the main concerns when implementing new technology is ensuring a smooth transition for workers who may not be used to handling digital tools. Weever's rollout methodology ensures that frontline workers can easily adopt and integrate the platform into their daily routines without disruption.
- Step-by-Step Rollout Plan: Weever's implementation process is structured in phases, starting with an introduction to the platform and gradually integrating it into the workers' everyday maintenance tasks. Workers are trained on how to access their CIL checklists, follow digitized CIL instructions, and manage their lubrication schedules. This phased approach ensures that workers aren't overwhelmed by the transition.
- Tailored Training: Weever offers CIL training for operators tailored to the specific industry in which they work. For example, food production workers receive training on how to adhere to strict cleaning standards, while retail workers are trained to maintain refrigeration and POS systems.
- Visual Controls for CIL: To further simplify task management, Weever offers visual controls for CIL, allowing workers to see at a glance what tasks are pending, completed, or require immediate action. These visual cues make it easy for workers to stay on top of their maintenance duties, even in busy environments like retail or logistics.
By providing a structured rollout plan, tailored training, and easy-to-understand visual controls, Weever ensures that frontline workers can seamlessly integrate the platform into their routines and start benefiting from its powerful features right away.
Streamlining Maintenance Routines with Weever's Connected Worker Platform
Managing maintenance routines doesn't have to be complicated. Weever's Connected Worker Platform simplifies the entire process, empowering frontline workers to take control of operator-led maintenance without needing advanced technical skills. From automating cleaning standards and inspection routines to tracking trends and providing real-time insights, Weever helps workers execute preventive maintenance by operators efficiently.
With an intuitive interface, automated workflows, and robust reporting tools, Weever ensures that frontline workers can handle maintenance tasks effectively, reducing equipment downtime and enhancing productivity. Its structured rollout methodology ensures a smooth transition, providing workers with the training and support they need to incorporate Weever into their daily routines seamlessly.
Weever's Connected Worker Platform is the key to streamlining maintenance processes, boosting productivity, and ensuring that maintenance tasks are always completed on time.
Ready to transform your maintenance routines with Weever's Connected Worker Platform?
Ready to transform your maintenance routines with Weever's Connected Worker Platform?
Continue Reading
"Having cloud-based forms on devices around the facility makes them so much more accessible, which makes it painless for operators to quickly provide a report."
Johanna Velez, VP Quality Assurance
"Weever is really user friendly and will have a massive positive impact on our operations and training team."
Mel Cadle - Op Ex Lead Process Engineer
"It's shifted our safety culture because now we are much more focused on what we should be looking at."
Kody Crossen, Operations Manager of EHS