Achieving Operational Efficiency with Weever: Integrating Centerlining, CIL, and 5S Audits
Achieve operational efficiency with Weever. Integrate Centerlining, CIL, and 5S audits to automate workflows, reduce waste, and drive continuous improvement.
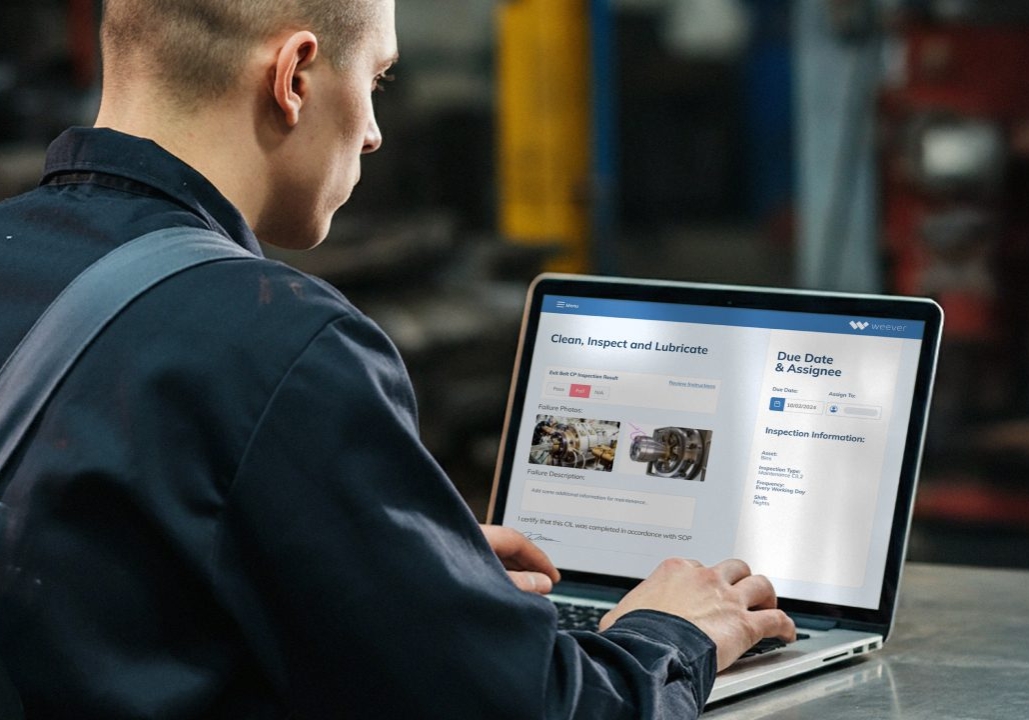
Operational efficiency is more than just a buzzword-it's a critical goal for manufacturers aiming to remain competitive in an increasingly demanding marketplace. Consistently producing high-quality products while minimizing downtime, waste, and variability requires a meticulous approach. Key methodologies such as Centerlining, Clean Inspect Lubricate (CIL), and 5S audits serve as foundational pillars of operational efficiency. However, implementing and maintaining these practices across teams and facilities is no small feat.
This is where Weever's software comes in. By providing an intuitive, integrated platform, Weever empowers manufacturers to seamlessly adopt and optimize these essential practices. In this blog, we'll explore the question: How can manufacturers achieve operational efficiency by integrating Centerlining, CIL, and 5S audits with Weever? Along the way, we'll uncover how Weever's innovative solutions simplify implementation, automate workflows, and provide real-time insights to ensure sustained efficiency and excellence.
Understanding the Role of Centerlining, CIL, and 5S Audits in Operational Efficiency
Before diving into the specifics of how Weever enhances these practices, it's important to understand their individual contributions to operational efficiency:
- Centerlining: This process involves setting and maintaining optimal equipment parameters to reduce variability in production. By adhering to precise settings, manufacturers can ensure consistent quality and minimize waste.
- Clean Inspect Lubricate (CIL): As a core component of autonomous maintenance, CIL emphasizes regular cleaning, inspection, and lubrication to keep equipment running smoothly. This proactive approach prevents unexpected breakdowns and extends equipment life.
- 5S Audits: Rooted in lean manufacturing principles, 5S audits focus on organizing and maintaining the workplace to improve efficiency and safety. The five pillars-Sort, Set in Order, Shine, Standardize, and Sustain-help create a clean, structured environment that minimizes errors and enhances productivity.
Individually, these practices drive significant benefits. Combined, they create a holistic framework for achieving and sustaining operational efficiency. However, traditional approaches to implementing these methodologies often face hurdles such as inconsistent execution, time-consuming manual processes, and limited visibility into results.
Weever eliminates these challenges by offering a unified platform to integrate, automate, and optimize Centerlining, CIL, and 5S audits.
Intuitive Integration with Weever's Platform
For any operational improvement initiative to succeed, teams must be able to adopt and integrate new practices with ease. This is especially true for methodologies like Centerlining, CIL, and 5S audits, which require consistent execution across shifts and teams.
Weever's software is designed with simplicity in mind. Its intuitive interface ensures that users at all levels-from shop-floor operators to managers-can navigate the platform and quickly implement these practices without extensive training.
- Centerlining: Setting up Centerlining parameters is straightforward with Weever. Teams can configure optimal settings for equipment, define acceptable ranges, and establish alerts for deviations-all within a few clicks.
- CIL: Weever makes scheduling and executing CIL tasks effortless. Teams can create detailed checklists for cleaning, inspecting, and lubricating equipment, ensuring that nothing is overlooked.
- 5S Audits: The platform enables manufacturers to configure 5S checklists, making it easy to assess workplace organization and address areas for improvement.
This simplicity reduces the learning curve, accelerates adoption, and allows teams to focus on execution rather than struggling with complex software.
Automation in Action: Driving Consistency and Efficiency
Consistency is a cornerstone of operational efficiency, and Weever ensures that key practices are carried out reliably through automated workflows.
- Centerlining: Once parameters are defined, Weever monitors equipment settings in real time, automatically flagging deviations and notifying teams to take corrective action. This ensures that production remains within optimal ranges, reducing variability and waste.
- CIL: Routine maintenance tasks are automated with Weever, from scheduling to tracking completion. The software sends reminders for cleaning, inspection, and lubrication activities, ensuring that critical tasks are performed on time. Deviations or abnormalities discovered during inspections can be documented and escalated for prompt resolution.
- 5S Audits: Weever streamlines 5S audits by guiding teams through standardized checklists and assigning follow-up tasks for any deficiencies identified. Automated notifications keep audits on schedule, ensuring that workplace organization is maintained consistently.
By eliminating manual intervention and providing automated oversight, Weever reduces the risk of errors, ensures timely execution, and frees up teams to focus on value-added activities.
Insight-Driven Decision Making: Leveraging Data for Improvement
Operational efficiency is not a one-time achievement-it requires ongoing monitoring and continuous improvement. Weever provides manufacturers with the tools to achieve both through powerful data-driven insights.
- Centerlining: Weever collects and analyzes data from equipment settings, enabling teams to identify trends and recurring deviations. For example, patterns of variability might point to the need for equipment recalibration or operator training.
- CIL: Insights from CIL tasks help manufacturers track the health of their equipment over time. Teams can use this data to identify components that require frequent maintenance, schedule predictive maintenance activities, and reduce unplanned downtime.
- 5S Audits: Weever provides actionable insights from 5S audit data, helping teams identify common organizational issues and measure the impact of improvements over time.
Real-time reporting further enhances visibility by providing up-to-the-minute updates on the status of Centerlining, CIL, and 5S activities. This immediacy enables manufacturers to respond quickly to deviations or gaps, ensuring that operational efficiency is maintained without disruption.
Standardized Excellence: Consistency Across Teams and Facilities
Implementing Centerlining, CIL, and 5S audits across a single production line is challenging enough; scaling these practices across multiple teams or facilities introduces even greater complexity. Weever addresses this challenge with a structured rollout methodology that ensures consistency and standardization.
- Templates and Standardized Workflows: Weever provides pre-configured templates and workflows for each practice, ensuring that every team follows the same high standards.
- Configurable Framework: While standardization is key, Weever's platform is also flexible enough to accommodate unique operational needs. Teams can configure workflows and parameters without compromising consistency.
- Scalability: Whether rolling out these practices across a single site or a global network of facilities, Weever makes it easy to scale operations and maintain uniformity.
This approach ensures that operational efficiency becomes a company-wide standard rather than being limited to isolated pockets of excellence.
Take the First Step Toward Transforming Operational Efficiency
The integration of Centerlining, CIL, and 5S audits with Weever delivers measurable results. By maintaining optimal equipment settings, manufacturers reduce variability, minimize waste, and ensure consistent quality. Proactive maintenance routines extend equipment life and reduce the risk of unplanned downtime. Meanwhile, a clean, organized workplace fosters safety, efficiency, and productivity.
Beyond these tangible benefits, Weever promotes a culture of accountability and continuous improvement. By automating workflows, providing actionable insights, and ensuring consistent execution, Weever helps manufacturers achieve operational efficiency and sustain it over time.
Operational efficiency is within reach when manufacturers have the right tools to support their efforts. By integrating Centerlining, Clean Inspect Lubricate (CIL), and 5S audits with Weever, teams can streamline workflows, make data-driven decisions, and create a culture of consistency and improvement.
Ready to see the difference Weever can make in your operations? Contact Weever today for a demo and discover how our software can help you achieve maximum operational efficiency.
Ready to optimize operations and reduce waste?
Ready to optimize operations and reduce waste?
Continue Reading
"Having cloud-based forms on devices around the facility makes them so much more accessible, which makes it painless for operators to quickly provide a report."
Johanna Velez, VP Quality Assurance
"Weever is really user friendly and will have a massive positive impact on our operations and training team."
Mel Cadle - Op Ex Lead Process Engineer
"It's shifted our safety culture because now we are much more focused on what we should be looking at."
Kody Crossen, Operations Manager of EHS