Automating 5S Audits with Weever for Consistent, Accurate Results
Automate 5S audits with Weever for accurate, consistent results. Simplify workflows, track trends, and improve workplace organization and efficiency effortlessly.
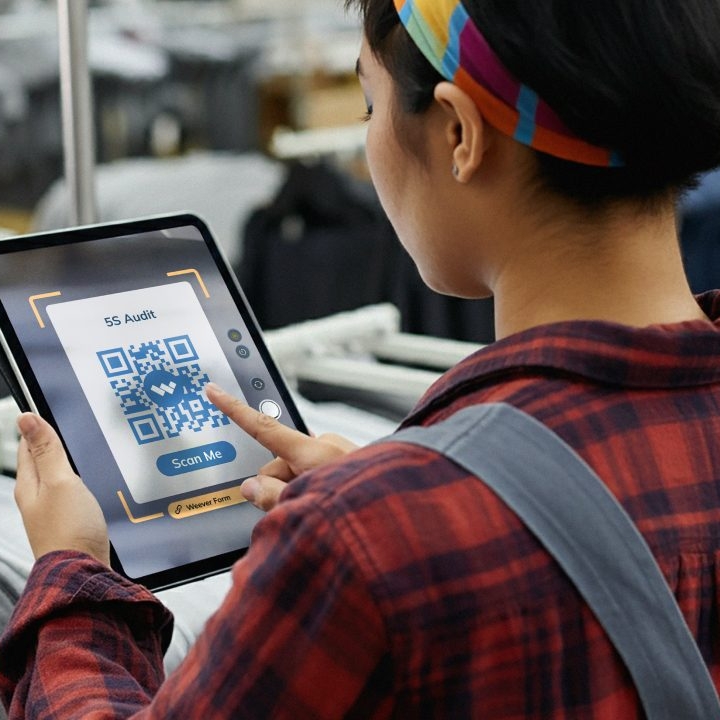
5S Overview
5S Planning
5S Implementation
5S Auditing
5S Audit Digitization
FREE RESOURCEs
Maintaining standards in manufacturing that deliver consistent, accurate results requires regular audits to ensure adherence and uncover opportunities for improvement. Traditional audit processes often rely on manual tracking and data entry, which can lead to inconsistencies, delays, and missed action items. The 5S methodology-Sort, Set in Order, Shine, Standardize, and Sustain-has become a cornerstone of workplace organization and efficiency in manufacturing. Its principles help create cleaner, safer, and more efficient work environments.
Weever software transforms the 5S auditing process by introducing automation, making it easier to schedule, execute, and follow up on audits. With streamlined workflows and real-time insights, Weever ensures consistent, accurate results that drive workplace efficiency. Let's explore how automating 5S audits with Weever makes this possible.
A Platform That Simplifies Audits for Everyone
For 5S audits to be effective, they need to be easy for employees to perform regularly. Complex systems or extensive training requirements can deter teams from conducting audits consistently, undermining the benefits of 5S. Weever addresses this challenge with a platform designed for simplicity and ease of use.
Weever's intuitive interface allows employees to complete 5S audits quickly and with minimal effort. Pre-configured checklists guide users through the process, ensuring that every aspect of the 5S methodology is addressed. Whether employees are using a desktop computer or a mobile device, they can log observations, document findings, and submit audit results in real time. This accessibility reduces the time spent on audits and ensures that all team members can participate, regardless of their technical expertise.
By making audits straightforward and user-friendly, Weever helps foster a culture of accountability and consistency. Employees can focus on upholding 5S standards rather than struggling with cumbersome audit tools.
Keeping the Process Consistent with Automation
Manual 5S audit processes often leave room for inconsistency and oversight. Missed deadlines, unclear responsibilities, and incomplete follow-ups can erode the effectiveness of the methodology. Weever's automation features ensure that every step of the audit process is executed reliably and on schedule.
With Weever, audits are automatically scheduled at regular intervals, so teams never miss a review. Tasks are assigned to the appropriate personnel, ensuring clarity and accountability. When abnormalities or defects are identified during an audit, the system generates actionable follow-up items and tracks them to completion. This eliminates the guesswork associated with manual tracking and ensures that every issue is addressed promptly.
Automation not only saves time but also reduces the risk of human error. By providing a standardized process for conducting and managing audits, Weever ensures consistency across teams and departments.
From Data to Decisions: Real-Time Insights and Trend Analysis
The value of 5S audits lies in the insights they provide into workplace organization and cleanliness. Conducting an audit is only the first step-analyzing the data and using it to drive improvements is where the real impact is made. Weever helps manufacturers unlock the full potential of their 5S audits by delivering real-time insights and trend analysis.
Weever's platform provides instant access to audit results, enabling teams to address any abnormalities or defects as soon as they are discovered. Comprehensive reporting tools make it easy to identify recurring issues and track improvement over time. For example, managers can use visual dashboards to monitor trends in workplace cleanliness or evaluate the frequency of specific deviations. This data-driven approach allows manufacturers to make informed decisions and implement targeted improvements.
With Weever's insights, teams can shift from a reactive approach to a proactive one. Instead of simply addressing problems as they arise, they can anticipate and prevent future issues, leading to a more stable and efficient workplace.
Standardizing Excellence Across the Organization
For manufacturers with multiple facilities or departments, achieving consistency in 5S audits can be a challenge. Variations in audit methods or standards can lead to discrepancies that undermine the effectiveness of the program. Weever's structured rollout methodology ensures that automated 5S audits are implemented smoothly and consistently across the organization.
Weever's rollout process begins with a seamless integration into existing workflows, minimizing disruptions to day-to-day operations. Predefined templates and checklists ensure that every team follows the same audit procedures, creating a unified approach to 5S. To support adoption, Weever provides training resources and ongoing support, helping employees quickly adapt to the new system.
By standardizing the 5S auditing process, Weever creates a foundation for consistent workplace organization and cleanliness. Teams across different locations or shifts can operate under the same high standards, fostering a company-wide commitment to efficiency and safety.
The Impact of Automating 5S Audits with Weever
Automating 5S audits with Weever goes beyond simplifying the process-it fundamentally transforms how manufacturers maintain workplace organization and efficiency. With a platform that combines ease of use, automation, real-time insights, and consistent implementation, Weever ensures that 5S principles are upheld and improved over time.
How Weever Supports 5S Audits:
- User-Friendly Interface: Reduces complexity and makes audits accessible to all employees.
- Automation: Ensures regular scheduling, clear task assignments, and effective follow-ups.
- Real-Time Data and Trends: Provides actionable insights to drive continuous improvement.
- Consistent Rollout: Standardizes audit practices across teams and facilities.
By reducing reliance on manual processes and equipping teams with powerful tools, Weever enables manufacturers to achieve consistent, accurate results that support a cleaner, safer, and more efficient workplace.
Take the Next Step Toward Workplace Excellence
Ready to revolutionize your 5S auditing process? With Weever, you can automate audits, improve consistency, and gain valuable insights that drive continuous improvement. Contact us today to request a demo and see how Weever can help your organization maintain the highest standards of workplace organization and efficiency.
Read our Ultimate Guide for 5S Auditing
Continue Learning about 5S
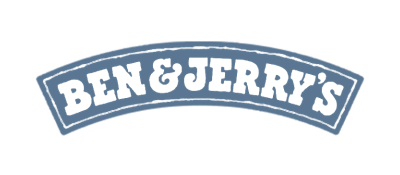
bandjlogo

Bell-logo-New
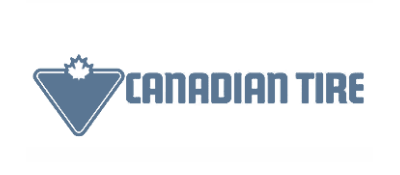
Canadian-Tire-Logo

Diageo-customer-logo

greyston-bakery-logo

hello-fresh-customer

marks-customer-logo

CSL_Limited_logo

monin-logo

Winland Food
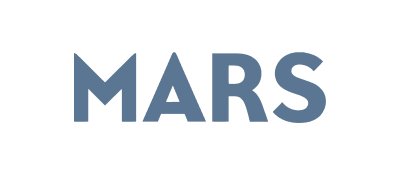
Mars-logo-main
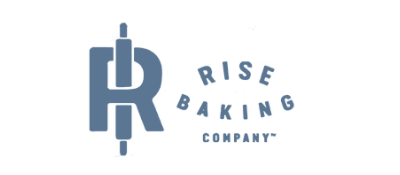
rise-baking-customer-logo

Rockwool-Customer-Logo-min
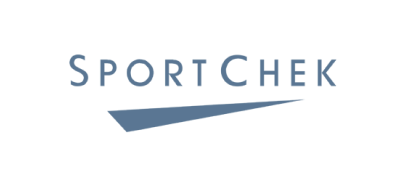
Sportcheck-customer-logo
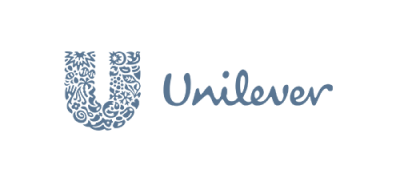
unilever-customer-logo

walmart-logo-small

husqvarna-customer-logo

Ajinomoto_logo
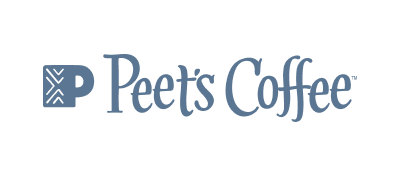
Peet's_Coffee_logo
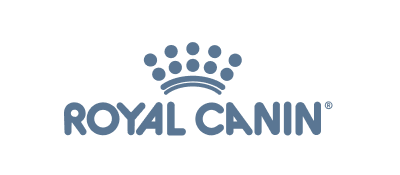
Royal-Canin-Logo