Optimizing Workplace Safety and Efficiency with Weever's 5S Audits
Optimize workplace safety and efficiency with Weever's automated 5S audits. Simplify processes, track insights, and ensure consistent, proactive improvements.
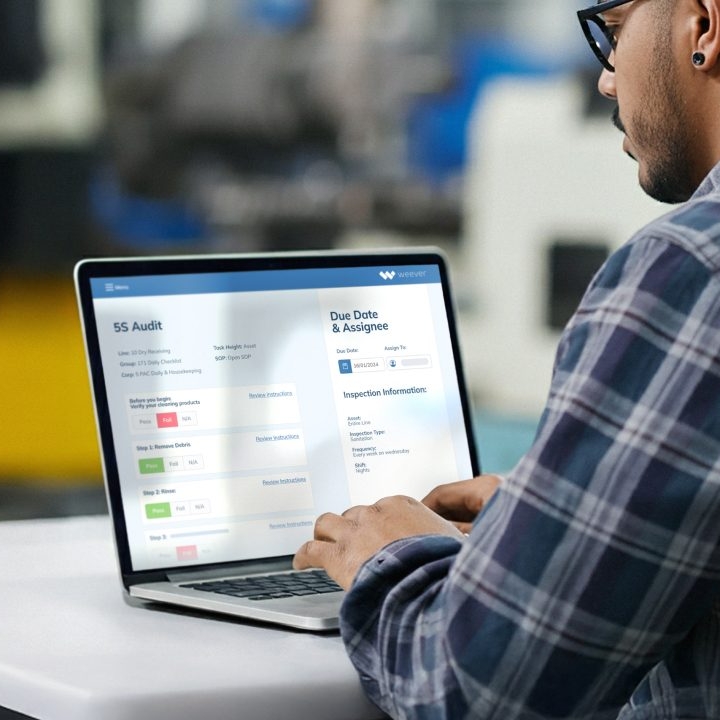
5S Overview
5S Planning
5S Implementation
5S Auditing
5S Audit Digitization
FREE RESOURCEs
Workplace safety and efficiency are foundational to success in manufacturing and industrial environments. One proven methodology for achieving these goals is the 5S framework-Sort, Set in Order, Shine, Standardize, and Sustain. When applied effectively, 5S principles create cleaner, safer, and more organized workplaces, driving productivity and minimizing risks. However, maintaining these standards requires regular, thorough audits to ensure compliance and continuous improvement.
Weever software transforms how manufacturers conduct 5S audits, offering a streamlined, automated solution that makes the process simpler, faster, and more effective. By digitizing 5S audits and providing real-time insights, Weever empowers organizations to optimize workplace safety and efficiency like never before.
So, how do Weever's 5S audits optimize workplace safety and efficiency? Let's take a closer look at how the Weever platform supports each stage of the process.
Simplifying 5S Audits with an Intuitive Platform
For 5S audits to be impactful, they need to be completed regularly by employees who understand their importance. However, complex or time-consuming audit processes can deter participation and result in inconsistent application. Weever solves this challenge with a user-friendly interface that makes 5S audits straightforward and accessible for all team members.
How Weever Simplifies 5S Audits:
- Ease of Access: Weever's platform provides employees with pre-configured 5S checklists that are clear and easy to follow, eliminating confusion during audits.
- Mobile-Friendly Functionality: Audits can be conducted directly from mobile devices, allowing employees to complete them on the shop floor without disrupting workflow.
- Minimal Training Requirements: The platform's intuitive design means new users can quickly learn how to navigate the system and perform audits efficiently.
By reducing the complexity of 5S audits, Weever ensures that teams can complete them consistently without compromising productivity. This simplicity encourages widespread adoption of the platform, helping manufacturers maintain high safety and efficiency standards across their workforce.
Staying on Track with Audit Automation
Even with the best intentions, manual 5S audit processes can result in missed tasks, delays, and incomplete follow-ups. Weever eliminates these pitfalls by automating key aspects of the 5S audit process, ensuring that everything stays on schedule and that no detail is overlooked.
Weever's Automation Features:
- Scheduled Audits: The platform automatically schedules 5S audits at regular intervals, ensuring they occur consistently without manual reminders.
- Task Assignments: Responsibilities for specific audit tasks are automatically assigned to the appropriate team members, improving accountability.
- Action Item Tracking: When issues such as safety hazards, cleanliness gaps, or inefficiencies are identified during an audit, Weever creates actionable tasks and tracks their progress until resolution.
Automation ensures that all aspects of the 5S audit process are completed on time and to standard. By removing the manual burden of managing schedules and action items, Weever enables teams to focus on resolving issues and improving workplace safety and efficiency.
From Insights to Impact: Unlocking the Power of Real-Time 5S Audit Data
While completing audits is important, the true value of 5S lies in the insights gained from the process. Weever goes beyond simple compliance checks, offering detailed analytics and real-time reporting that help manufacturers uncover trends, address recurring issues, and make proactive improvements.
Key Benefits of Weever's Insights and Real-Time Reporting:
- Immediate Feedback: Audit results are instantly accessible through the platform, allowing teams to respond quickly to potential risks or inefficiencies.
- Trend Identification: Over time, Weever's analytics reveal patterns in workplace organization and safety, such as frequently missed cleanliness standards or recurring hazards in specific areas.
- Improvement Tracking: Weever allows manufacturers to monitor their progress in maintaining 5S principles, ensuring sustained improvements in safety and efficiency.
By turning audit data into actionable insights, Weever helps organizations take a proactive approach to workplace safety and efficiency. Instead of simply reacting to issues, teams can anticipate and address potential problems before they escalate.
Consistency Across Teams for Uniform Standards
Implementing 5S audits across a large organization with multiple departments or facilities can be a logistical challenge. Variations in audit processes or standards can result in inconsistencies that undermine the effectiveness of the methodology. Weever's structured rollout plan addresses these challenges by ensuring a smooth and uniform implementation.
How Weever Supports a Successful Rollout:
- Seamless Integration: The platform integrates easily into existing workflows, minimizing disruption during implementation.
- Standardized Procedures: Predefined checklists and templates ensure that all teams follow the same audit protocols, creating consistency across the organization.
- Comprehensive Support: Weever provides training materials and ongoing assistance to help teams quickly adapt to the new system and maximize its benefits.
With a consistent approach to 5S audits, manufacturers can maintain uniform safety and efficiency standards across all locations. This not only simplifies management but also fosters a cohesive organizational culture committed to continuous improvement.
How Weever's 5S Audits Drive Workplace Safety and Efficiency
Weever's innovative approach to 5S audits empowers manufacturers to uphold the highest standards of safety, cleanliness, and efficiency in their workplaces. By combining an intuitive platform, automated workflows, real-time insights, and a structured rollout plan, Weever ensures that 5S principles are applied consistently and effectively.
Why Manufacturers Choose Weever for 5S Audits:
- Ease of Use: Simplifies the auditing process, encouraging participation and consistent execution.
- Automation: Removes manual tracking burdens, ensuring timely and thorough completion of all tasks.
- Data-Driven Insights: Provides valuable analytics and real-time feedback to drive continuous improvement.
- Consistency: Standardizes audit practices across teams and facilities for uniform application of 5S principles.
With Weever, manufacturers can replace inefficient manual processes with a smarter, more effective approach to workplace organization and safety. This leads to cleaner, safer, and more productive environments that benefit employees and the business as a whole.
Ready to optimize workplace safety and efficiency with automated 5S audits? Discover how Weever's platform can transform your approach to 5S, providing the tools and insights you need to drive continuous improvement. Contact Weever to schedule a demo and take the first step toward a safer, more efficient workplace.
Read our Ultimate Guide for 5S Auditing
Continue Learning about 5S
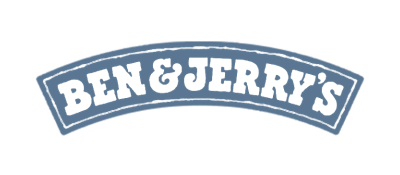
bandjlogo

Bell-logo-New
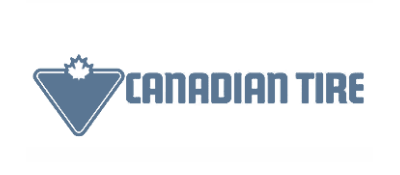
Canadian-Tire-Logo

Diageo-customer-logo

greyston-bakery-logo

hello-fresh-customer

marks-customer-logo

CSL_Limited_logo

monin-logo

Winland Food
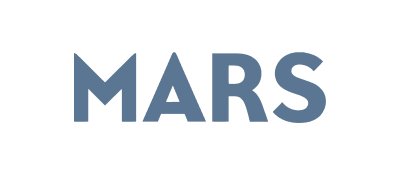
Mars-logo-main
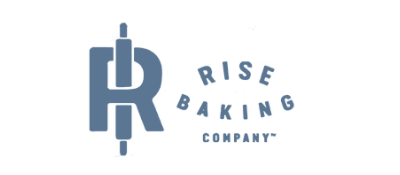
rise-baking-customer-logo

Rockwool-Customer-Logo-min
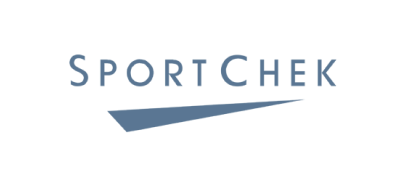
Sportcheck-customer-logo
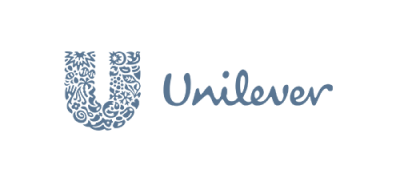
unilever-customer-logo

walmart-logo-small

husqvarna-customer-logo

Ajinomoto_logo
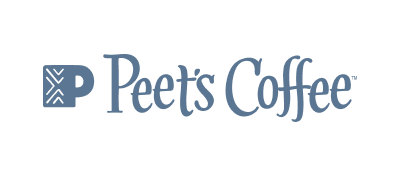
Peet's_Coffee_logo
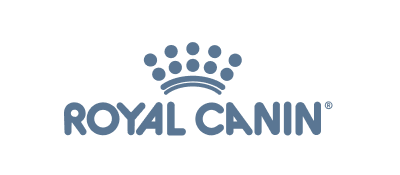
Royal-Canin-Logo