The Power of Proactive Measures in Preventing Equipment Failure
Learn to prevent equipment failures with proactive maintenance measures using Weever’s software, enhancing operational efficiency and safety.
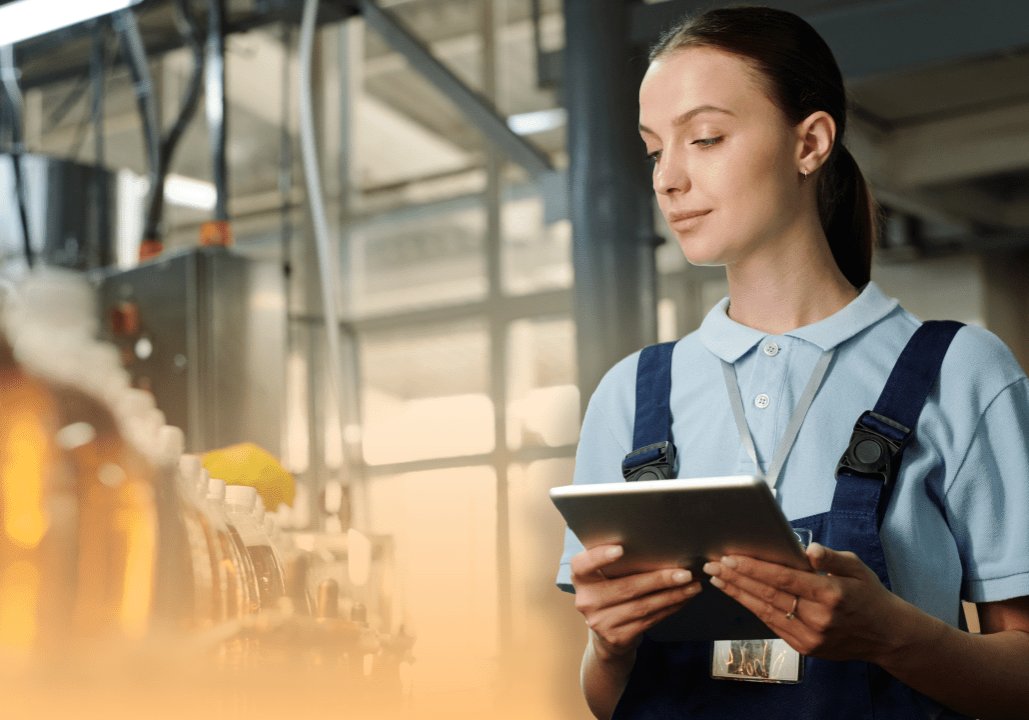
In any industrial setting, equipment maintenance is crucial for ensuring operational efficiency, safety, and longevity. The performance of machinery directly influences production rates, product quality, and workplace safety. Neglecting equipment maintenance can lead to unexpected breakdowns, which not only cause disruptions in the production line but also result in significant financial losses due to downtime and costly emergency repairs.
Proper maintenance helps in identifying potential issues before they escalate into major problems, and thus taking proactive measures allows for timely interventions that keep machinery running smoothly and efficiently. Moreover, regular maintenance schedules help extend the life of the equipment, optimize its performance, and reduce the likelihood of accidents caused by faulty machinery.
Weever is a leading solution provider that specializes in enhancing equipment reliability through proactive maintenance measures. With a robust platform designed to streamline maintenance processes, Weever offers a comprehensive suite of software tools that empower businesses to shift from a reactive to a proactive maintenance model.
Understanding Equipment Failure
Equipment failure occurs when machinery ceases to function as intended, leading to disruptions in production and potential safety hazards. The impact on business operations includes decreased productivity, increased operational costs, and potential loss of revenue. Common causes of equipment breakdown include wear and tear from regular use, improper handling by operators, running over capacity, and lack of regular maintenance. These factors can accelerate equipment degradation and lead to premature failure, underscoring the importance of adhering to proper usage guidelines and maintaining a rigorous maintenance schedule to ensure optimal equipment performance and longevity.
The Cost of Reactive Maintenance
Reactive maintenance, often termed "run-to-failure" maintenance, involves addressing equipment repairs only after a breakdown occurs. This approach contrasts sharply with proactive maintenance, which focuses on preventing failures before they happen through regular checks and predictive techniques. While reactive maintenance might seem cost-effective in the short term, it often results in higher overall costs. This is due to unforeseen emergencies that require immediate and costly repairs or replacements of components, often at premium rates.
Additionally, equipment breakdowns lead to unplanned downtime, reducing productivity and potentially delaying delivery schedules, which can erode customer trust and satisfaction. In contrast, proactive maintenance allows for the scheduling of maintenance tasks during off-peak times, minimizing disruption and maintaining continuous operational efficiency, ultimately saving costs associated with extensive repairs and lost productivity.
The Benefits of Proactive Maintenance
Adopting proactive maintenance strategies offers several advantages that significantly enhance operational efficiency and equipment longevity. Predictive maintenance, a key component of proactive strategies, utilizes data from equipment sensors to predict failures before they happen. This approach allows maintenance teams to address potential issues at the most opportune times, rather than reacting to unexpected breakdowns.
Condition monitoring further supports this by continuously checking the operational status of machinery through parameters like vibration, temperature, and sound. Real-time monitoring ensures that any deviation from normal performance is quickly detected and addressed, preventing minor issues from escalating into major failures. Together, predictive maintenance and condition monitoring ensure that equipment operates at peak efficiency, reduces the frequency of repairs, and extends the overall lifespan of machinery, leading to substantial cost savings and improved reliability.
Weever Facilitates Proactive Maintenance
Weever’s Autonomous Maintenance software solution equips businesses with a range of features and tools designed to support scaling proactive measures in regard to maintenance strategies. This results in frontline staff, supervisors, and managers all working together to enable a cycle of autonomous maintenance.
Frontline employees using machines and equipment daily are in the best position to continually monitor and upkeep it, much more so than an occasional audit or check-up by a dedicated technician. With Autonomous Maintenance, everyday equipment operators receive easy-to-follow instructions and tasks for taking proactive measures. When potential issues are identified, photos and videos can be captured and shared directly in the software to the relevant technicians.
Supervisors can use Autonomous Maintenance to enhance collaboration, team visibility, and increase ownership. They can create and manage action plans for dedicated maintenance teams and frontline staff. At a glance, supervisors can view the higher-level view of task statuses and lists, making decisions about proactive measures easier than ever.
Finally, managers and analysts enjoy automated reporting and trend analysis, generated from all of the data being collected at the lower levels of the business. This allows for continuous improvement in processes through updated standard operating procedures, as well as informing decision-making about taking proactive measures at the strategic level.
Implementing Proactive Measures with Weever
Implementing proactive measures with Weever involves a straightforward, step-by-step process to integrate advanced maintenance strategies into existing operations:
- Initial Setup: Begin by installing Weever software and configuring it to integrate with existing equipment and IT infrastructure.
- Inventory and Asset Tagging: Catalog all equipment and critical assets in the Weever software system, applying tags for easy identification and monitoring.
- Set Maintenance Baselines: Establish maintenance baselines and schedules based on manufacturer recommendations and historical data, using Weever’s scheduling tools..
- Monitor and Adjust: Adjust maintenance schedules as needed based on insights gained from ongoing analysis and reports.
Review and Optimize: Regularly review the performance analytics provided by Weever to optimize maintenance routines and improve overall equipment efficiency and reliability.
Avoid the Cycle of Reactive Maintenance
Adopting proactive maintenance measures with Weever not only enhances operational efficiency but also significantly reduces the risk of equipment failure. By transitioning from reactive to proactive maintenance, businesses can anticipate and mitigate issues before they disrupt production, thereby saving on costly repairs and downtime. Weever's Autonomous Maintenance software equips your team—from frontline workers to managers—with the tools necessary to monitor, maintain, and optimize equipment performance seamlessly.
Don’t let preventable failures set your operations back. Contact Weever today for a consultation or demo, and start transforming your maintenance processes. Discover how our innovative approach can make a significant difference in your equipment management and overall business success.
Interested in learning more about Weever's Proactive Safety Solution?
Download the Ultimate Guide
Everything you need to know about how implement a proactive safety program and the best practices gleaned from our 10+ years of experience helping organizations achieve success.
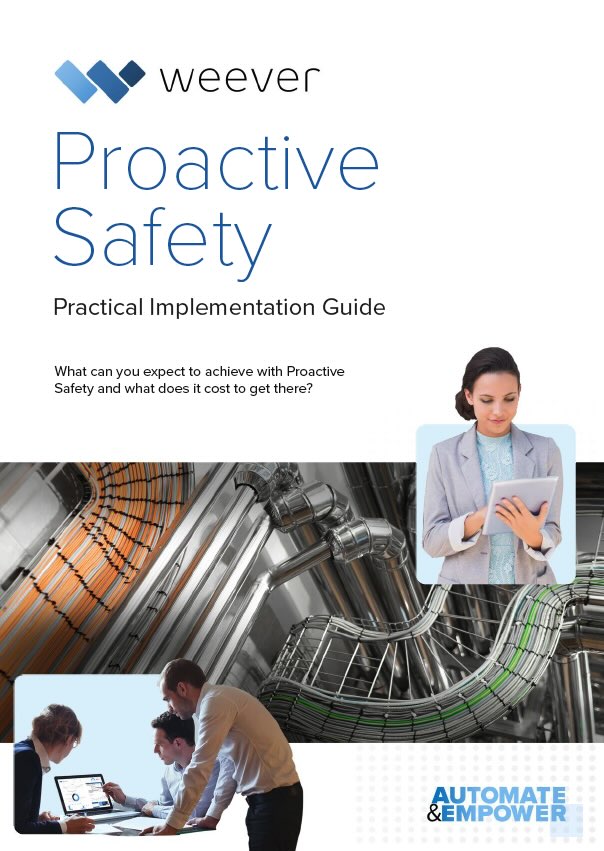
"It's easy to anticipate safety issues with Weever."
“In a warehouse setting it's very easy to fall into the trap of being reactive. With Weever we are 60-70% proactive. That's huge!"
Kody Crossen | Operations Manager of EHS, Walmart DC6080
Continue Reading about Proactive Safety
“Having cloud-based forms on devices around the facility makes them so much more accessible, which makes it painless for operators to quickly provide a report.”
Johanna Velez, VP Quality Assurance
"Weever is really user friendly and will have a massive positive impact on our operations and training team."
Mel Cadle - Op Ex Lead Process Engineer
“It’s shifted our safety culture because now we are much more focused on what we should be looking at.”
Kody Crossen, Operations Manager of EHS