Transforming Safety Observations at JERA Americas with Weever
How JERA Americas Enhanced Efficiency and Real-Time Visibility in Its Safety Observation Program using Weever.
weever case studies
Key Benefits:
- Automated data entry and processing eliminated the time-consuming manual re-entry of observations.
- Immediate access to safety observation data allowed for prompt identification and resolution of issues.
- Enhanced integration with PowerBI Reports provided clear and comprehensive data during monthly health and safety meetings.
- Exceptional support from Weever's Customer Success team ensured smooth implementation and ongoing success.
The Challenge
JERA Americas faced a significant challenge in managing its safety observation program due to its reliance on the Dupont system, which involved manual data entry using handwritten cards. This method was extremely time-consuming and labor-intensive, requiring staff to re-enter data digitally, which not only slowed down the process but also increased the risk of errors.
Additionally, the Dupont system lacked the flexibility and real-time visibility needed to promptly address safety issues as they arose, making it difficult for JERA to gain comprehensive insights into troubled areas within their operations.
Despite the process, the Canal station managed to achieve a 98% completion rate for its Behavior-Based Safety Observations (BBSO) program. This metric indicates a high level of engagement and thoroughness in recording observations. However, the manual nature of the system also highlighted the gap between the number of observations conducted and those that remained open, underscoring the need for a more streamlined and faster solution to close this loop and enhance overall safety performance.
The Implementation
The implementation of Weever's software at JERA Americas began with researching the best tools for the job, and realizing that Weever was the best solution for their safety observation needs.
The initial phase involved onboarding and training provided by Weever, which included instructional videos that demonstrated the program's straightforward nature.
The rollout commenced gradually, starting with the management team at the Canal station to ensure a thorough understanding of the features and functions. This step-by-step approach allowed the team to familiarize themselves with the robust capabilities of the program, facilitating a smooth transition from the previous manual system.
Following the successful initial rollout, JERA Americas began expanding the use of Weever to new applications in August 2023. Over the next nine months, they introduced a new use case called "Good Catch," although they faced some challenges with the Bucksport BBSO form. Despite these hurdles, the team remained committed to refining the implementation and planned to gain traction with the Good Catch form, demonstrating their ongoing efforts to enhance safety observation practices across the organization.
The Solution
JERA Americas' team experienced significant improvements with Weever's implementation. The program has, however, evolved from its original launch base-package to allow for additional insights, including monthly data evaluation and other necessary adjustments based on management feedback.
The support provided in getting the system up and running was tremendous; despite the challenges faced, the solution simply required user-friendly report tweaks.
The ability to send observation notes with positive reinforcements helps foster a healthy work environment, making the Weever software a great fit with no negative feedback. The Weever Customer Success Team was particularly helpful and responsive, ensuring complete satisfaction with the customer support provided.
The Results
The implementation of the Weever solution at JERA Americas has significantly improved information sharing across the organization.
The integration of PowerBI Reports for monthly Health and Safety (H&S) meetings has been extremely beneficial, providing clear and comprehensive data to support decision-making. The enhanced ability to share information efficiently has been highly valued, contributing to better visibility and management of safety observations. These improvements have not only streamlined operations but also fostered a culture of continuous safety enhancement within the organization.
The Conclusion
The adoption of Weever has had a profoundly positive impact on JERA Americas' safety observation program, transforming a previously labor-intensive and inefficient process into a streamlined and effective system.
The enhanced real-time visibility, improved information sharing, and robust support have significantly contributed to better safety management and compliance. The ongoing partnership between JERA and Weever promises further advancements, with plans to expand the use of the software and integrate additional features to drive continuous improvement.
Interested in learning more about Weever's ability to enhance production efficiency?
Explore Our Case Studies
"Having cloud-based forms on devices around the facility makes them so much more accessible, which makes it painless for operators to quickly provide a report."
Johanna Velez, VP Quality Assurance
"Weever is really user friendly and will have a massive positive impact on our operations and training team."
Mel Cadle - Op Ex Lead Process Engineer
"It's shifted our safety culture because now we are much more focused on what we should be looking at."
Kody Crossen, Operations Manager of EHS
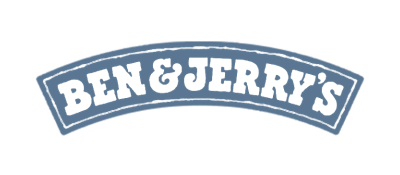
bandjlogo

Bell-logo-New
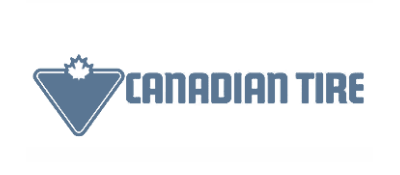
Canadian-Tire-Logo

Diageo-customer-logo

greyston-bakery-logo

hello-fresh-customer

marks-customer-logo

CSL_Limited_logo

monin-logo

Winland Food
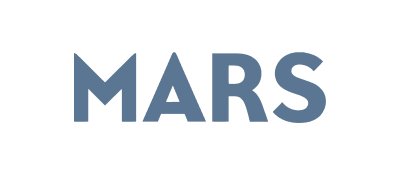
Mars-logo-main
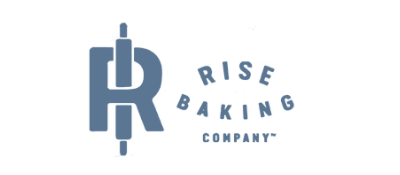
rise-baking-customer-logo

Rockwool-Customer-Logo-min
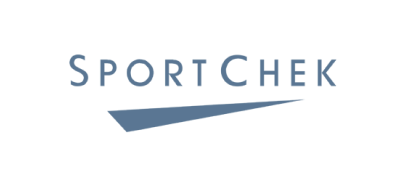
Sportcheck-customer-logo
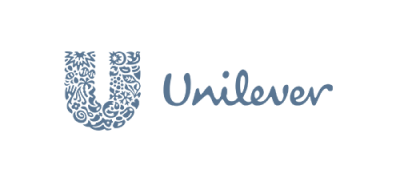
unilever-customer-logo

walmart-logo-small

husqvarna-customer-logo

Ajinomoto_logo
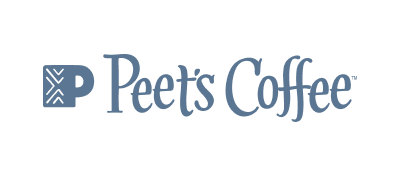
Peet's_Coffee_logo
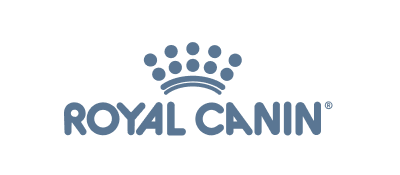
Royal-Canin-Logo